Strip Processing Plants or Lines Lines, Strip Cleaning Plants, Strip Coating Plants and Strip Annealing Plants - Overview
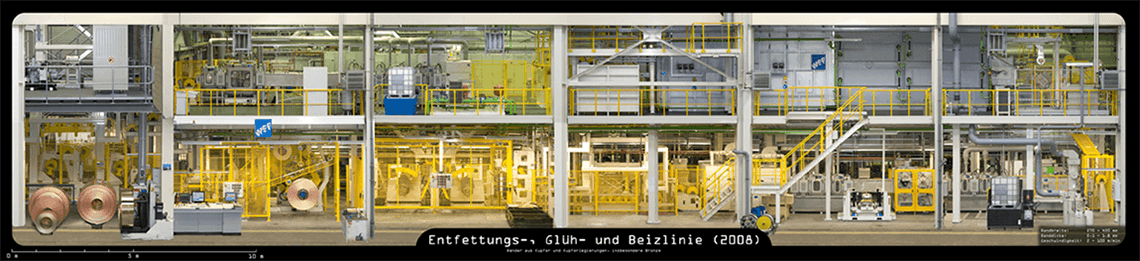
Strip Processing Plant or Line - Term and Structure
A strip plant executes at least one process step with a coiled metal strip.
The basic structure of a strip plant is always identical:
Decoiling area with at least one decoiler, strip shear, drive roll and usually a strip connecting device.
Processing area (strip processing, strip treatment, strip coating, strip annealing)
Coiling area with a strip shear, drive rolls and at least one coiler
Examples of Strip Processing Plants or Lines:
- Rewinding Lines unwind a coil by a decoiler and rewind it by a coiler. Meaning, the previously inner windings are outside now.
- Stretch Levelling Lines change the characteristics of metal strips by operating with a high strip tention. Simultaneously, the strip is bent around relatively small roller diameters. Thereby, characteristics like the yield strength can be influenced.
- Seaming Plants cut the sides of the metal strips. - A cross-cut line cuts the web-shaped metal strip into sheets.
- A slitting line („shear line“) cuts the strip into longitudinal parts that are then rewound on a common or single coiler.
Strip Treatment Plant or Line: Degreasing Plant, Strip Cleaning Plant, Pickler, Brushing Plant and Brushing Machine for metal and metal strip
A strip treatment plant changes the surface characteristics of metal strips.
For example, strip cleaning plants clean the strip surface. Depending on the type of contamination, alcaline or acidic degreasers or picklers are used. In special cases, also electrolytic or ultrasonic degreasing systems are needed. The typical purpose of picklers is to reduce the amount of oxides on the strip surface. This process can also be electrolytically supported. Most common in the fon-ferrous metal sector are sulfuric acid picklers.
Abrasive brushing machines or polishing machines grind or polish the strip surface. For this purpose, the brushing machines are equipped with roller brushes or fleece brushes. Please check on “WSP Brushing Machines” for this topic. The last step after pickling or brushing is often passivation, in order to prevent the bare strip material from oxidation.
Strip Coating Plants: Coating Process and Strip Dryer
Strip coating plants apply a coating medium of a defined thickness by various methods (e.g. roll coating or coating knife). Afterwards, the coating medium is dryed. The applied medium can be water-based or solvent-based. In case of the latter, it must be ensured that no hazardous enrichment of solvents in the dryer atmosphere can occur. The drying process is typically convective (convection dryer, usually energy-saving) by radiation (IR-radiation dryer).
Strip Annealing Line
In a strip annealing line the strip is subjected to heat treatment. The annealing process is executed, for example, for intermediate annealing (soft annealing) between the individual rolling steps in order to allow a new cold deformation for any following rolling steps. A strip cleaning device is often installed in front of the furnace to remove the adhering rolling oil. Since the annealing process can also lead to oxide formation on the strip suface (e.g. during the annealing of brass or nickel silver), a pickler is usually installed behind the furnace, followed by brushing machines and a passivation. This last step is also called finishing or finish treatment. Especially when the last step in strip production is the annealing process, the finishing is of great importance: the surface characteristics of the strip are determined by the pickler, the abrasive brushing machines as well as by the passivation and the drying process.
Non-ferrous metal annealing plants differ from steel annealing plants mainly for three reasons:
- Non-ferrous metals have very low absorption levels. A powerful furnace must, therefore, deliver the energy to the good primarily by convection.
- Non-ferrous metals are extremely sensitive at high temperatures; at the same time the surface requirements are very high. For this reason, non-contact processing inside the furnace is very important for non-ferrous metals.
- The demand for non-ferrous metals is, compared to the steel sector, significantly lower. In addition, copper as a raw material is very expensive. The copper price has been between 6,000 and 10,000 € in recent years.
Strip Plant Concept: Endless Strip or Individual Feeding
In a strip plant, one coil can be connected to the next coil by means of a strip connecting machine. This mode is also called “Endless Strip Processing”. However, if the tape runs completely through the plant without being connected to the new strip, it is called “single-feed”. In this case, the following strip must be newly pulled or pushed through the plant. Rewinding plants, stretch levelling plants, seaming plants and slitting machines are often single feeders. However, most strip treatment plants, coating plants or annealing lines are designed as endless strip systems.
Strip Treatment Concept: Discontinuous or Continuous Strip Plant
An additional distinguishing feature concerns the operation mode in the process section. Endless strip plants can be operated discontinuously or continuously. In a continuous strip plant, the strip is continuously in motion in the process section, even if the coil in the unwinding (decoiling) area has just run empty. While the connection with the new strip is now made in the decoiling area, the process zone is provided with strip material from a strip accumulator. In order to build this accumulator as compact as possible, the strip connection must be made as quick as possible. Plants, for which a short standstill in the process part is not critical, can also be designed as a discontinuous system. Here, the strip stops in the process section for the time of connection.