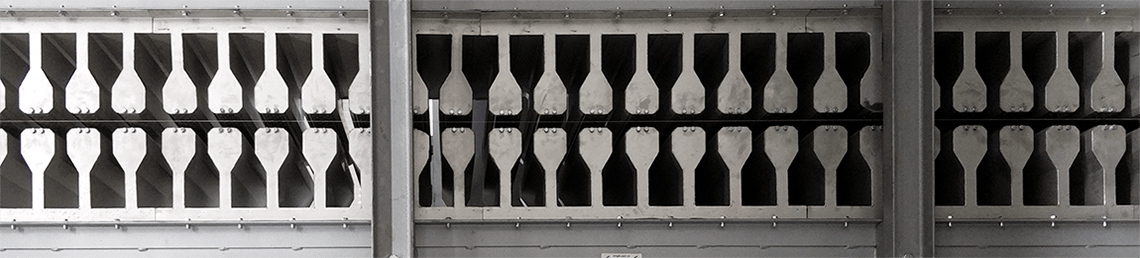
Cooling Sections in Continuous Annealing Lines for Stainless Steel Strips
In WSP High Performance Floatation Cooling Zones the strip is cooled down with air behind the furnace (contactless). The improved nozzle system reduces shape distortion when thin strips are cooled down and prevents strip oscillation.
Optionally, the strip can be transferred at the furnace exit by means of a floating deflector roller which replaces the normal furnace roller there.
Cooling Sections in Tinning Lines, Galvanization Plants and Aluminizing Lines
These cooling sections are usually fed with ambient air. They reach very high cooling rates, but do not blow off the sensitive, sometimes still liquid layers. For vertical strip cooling plants WSP installs nozzle systems similar to those used for horizontal floatation furnaces. Forces applied to the strip by these nozzles lead to an improved strip stabilization and a considerably smoother strip in the cooling section even for vertically guided strips. The nozzles can be located closer to the strip surface in order to improve the heat transfer. The cooling plants operate with relatively low nozzle exit velocities. They are, therefore, best suited for cooling down coated strips due to the low risk of blow-off.
Protective Gas Cooling Sections in Strip Lines
Strips can be cooled down in WSP-protective gas cooling sections with horizontal or vertical strip run. By using protective gas which contains up to 100% H2, very high cooling rates (which are required for special alloys) can be economically achieved.
Water Cooling Sections in Strip Lines
The cooling power of WSP Water Cooling Lines for steel strips can be perfectly controlled. Very uniform cooling is achieved by the special selection and arrangement of spray nozzles. Optionally, the water cooling section can also be operated as an immersion cooling (submerged spray nozzles).
WSP air cooling plants are designed
*for moderate nozzle exit velocity at high heat transfer *for relatively low input power of the supply air fans *for high circulated gas volume flow for uniform cooling *with stable nozzle constructions without protruding edges, plates or pipes *with improved nozzle systems for perfect strip stability and flatness after cooling